Knowledge update
Optimise your stock management.
Automation issue in your warehouse?
How do you keep a grip on the stock?
Your e-fulfilment business is growing. Your customer base is growing. But more customers also means more product inventory. Moving to a larger building may seem obvious, but it is not always an option. If a new building or move is not possible for the time being, you will have to make optimal use of the available space. That means: optimizing the way of stock storage. But how?
Step 1: inventory customer file.
The first step is obvious: make an inventory of the customer base. What kind of customers do you have, which orders are placed, how large are those orders, both in volume and size. What is the promised delivery time? You put all this data together in one file. This gives you a complete overview and you can continue.
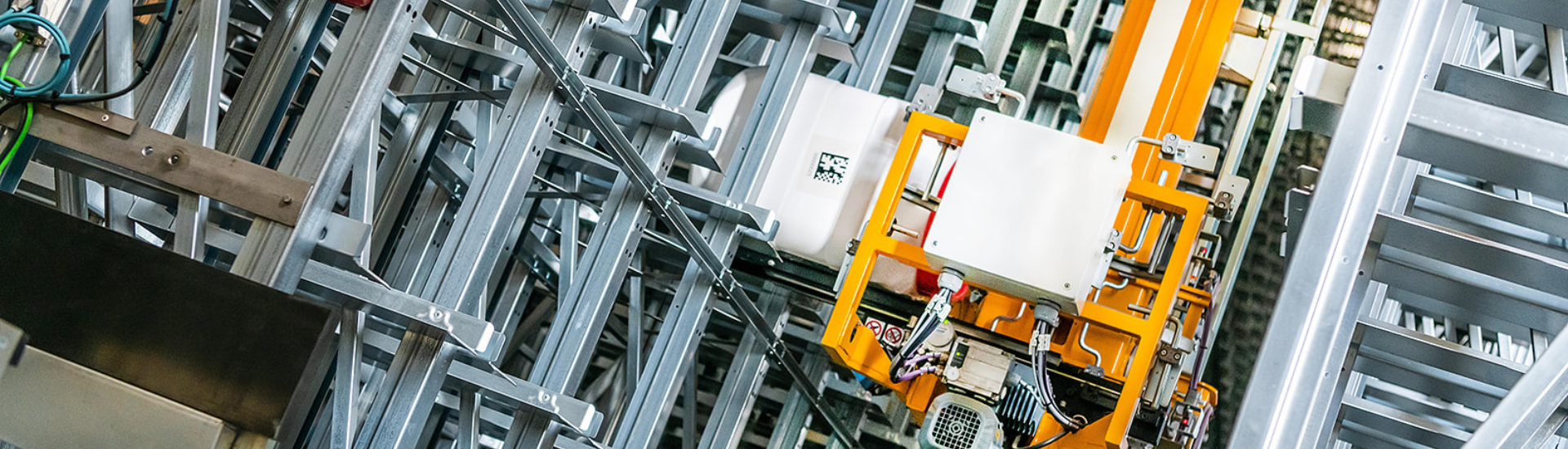
Step 2: runners.
Which products are ‘runners’? Which products are ordered incidentally? Can I put the runners close together? Does that fit in terms of size, in terms of volume. Putting the fast-moving products together has the advantage that order pickers can work more efficiently and faster. They don’t have to move from one side of the building to the other in a short time. It goes without saying that the products that have a longer lead time can be placed at a location further down the warehouse. By means of a good registration system, for example bar coding, the order pickers know where the products are.
Step 3: save compactly.
How compact can I store? View the warehouse. Is the height of the building fully utilized? Or is there still room to build a floor? If the warehouse is high enough, you can consider installing a mezzanine floor. By placing a floor you use the space and your warehouse is doubled in storage capacity in one fell swoop. You connect the floor to the ground floor with lifts and/or conveyor systems. Or are the orders many single pieces? Then you can think of a mini load system. This is a compact warehouse system. The products are placed in bins and are automatically brought to the order pickers by a lift system.
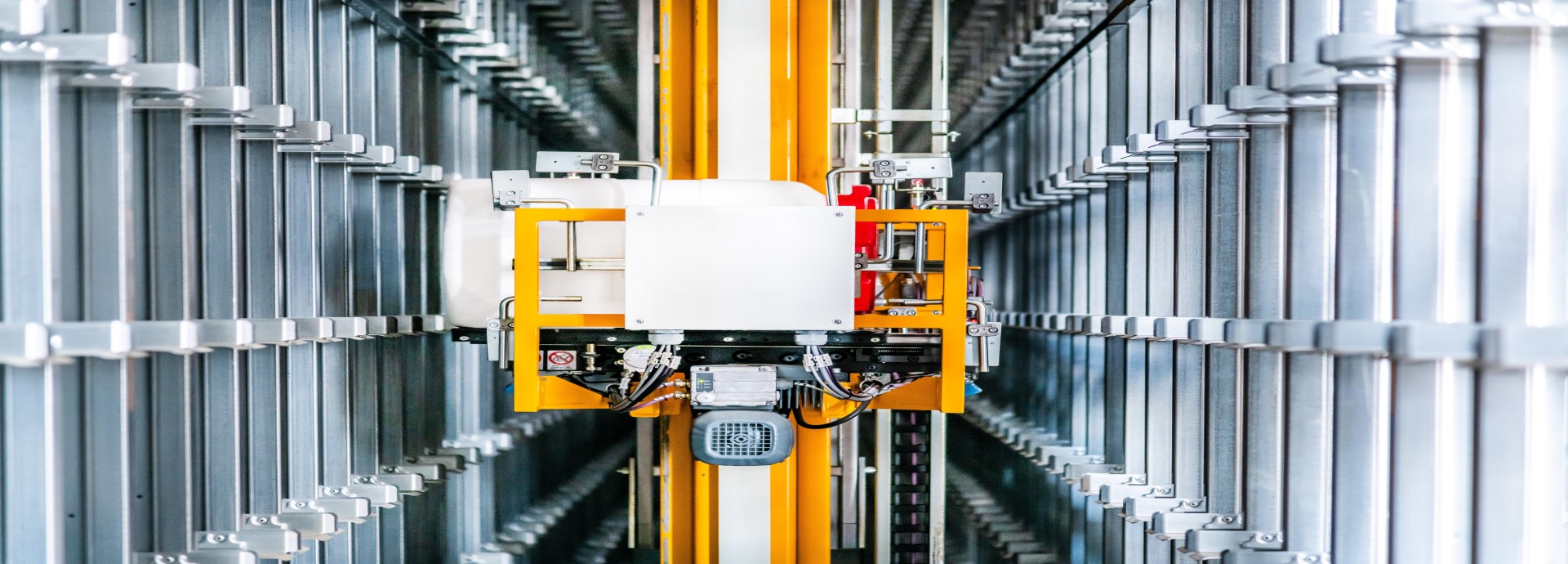
Step 4: the right WMS.
Find out and look for a party that can advise you and help you optimize your stock. If you have already taken the steps above, you can look more specifically for a party that can deliver what you are looking for. Visit comparable companies and be informed by ‘colleagues’ who have already gone through the inventory optimization process. That way you make the right choices.
Step 5: visit References.
Find out and look for a party that can advise you and help you optimize your stock. If you have already taken the steps above, you can look more specifically for a party that can deliver what you are looking for. Visit comparable companies and be informed by ‘colleagues’ who have already gone through the inventory optimization process. That way you make the right choices.
COSTO Intralogistics expertise in practice.
Get inspired by one of our other projects!
Service and Support
Subscribe to our newsletter.
"*" indicates required fields