Knowledge update
What is warehouse automation?
Learn more about warehouse automation.
Warehouse automation.
Warehouse automation includes all automation efforts to make the warehouse more efficient. Warehouse automation has two main features: the hardware focuses on the equipment in the warehouse and the software focuses on the proper control of this equipment.
What are the benefits of warehouse automation?
There are various reasons for choosing warehouse automation. There is a suitable automation solution for every warehouse.
The main advantages of warehouse automation are:
- Improved warehouse efficiency
Through smart applications in automation, a higher efficiency is achieved. Intelligent software calculates the optimal and quickest route. - Increased speed
Equipment works ultra-fast 24 hours a day, 7 days a week. Compared to a warehouse worker, an automated system processes up to four times as many orders. - Error reduction
Machines do not make mistakes in order picking. Therefore warehouse automation drastically reduces errors. - Cost reduction and ROI
For most warehouses the ROI of warehouse automation is the important benefit. The benefits listed above, combined with reduced personnel costs (FTE reduction), form the basis for a strong cost reduction.
What are the benefits of warehouse automation for employees?
Automation is sometimes misrepresented as replacing personnel and therefore jobs. However, the reality is that there is a huge shortage of warehouse personnel. In addition, automation also provides strong benefits for staff, including:
- Work content improvement
Because staff have to do less repetitive work, the challenge and pleasure in their work improves. - Improved safety
Allowing the machine to do the work reduces the risk of accidents during order picking. - Ergonomic improvement
By reducing the physical strain on staff, the ergonomic conditions of the warehouse are improved.
What types of warehouse automation are there?
Warehouse automation is characterised by two different types, namely ‘goods to person’ and ‘person to goods’. These types are applied individually or in combination, whereby a properly functioning software system is essential for control.
Goods to person refers to all intralogistics systems that transport goods to the warehouse operator. Goods to person solutions minimise the time spent by employees, make your warehouse more compact and increase efficiency. Some forms of goods-to-person solutions are:
- Order picking robots
Order picking robots pick a rack in its entirety and drive it to a central point. An employee then picks all orders from the rack and the robot drives the rack back into place. - Mini loads
Mini loads refer to the automatic loading and unloading of totes, trays or boxes in a compact space. The order is picked from small compartments with a mini load crane and delivered to a conveyor belt or picking station. - Platform lifts
A platform lift is often used for the storage of smaller items. These items are usually stored in special containers on a platform which in turn are divided into several drawers. The platform is sent down, after which the order picker picks the right items. - Shuttle
A shuttle automatically transports totes, boxes or trays to one or more picking stations in a shuttle system. The inbound and outbound movements to and from the rack frame are fully automatic. The shuttle system combines various intralogistic systems.
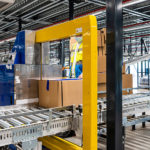
Person to goods
Person to goods refers to all intralogistic systems that ensure optimal order picking by the warehouse employee. Person to goods solutions reduce picking errors, increase efficiency and support your warehouse employees. Some forms of ‘person to goods’ solutions are:
- Zone picking
With zone picking, orders are transported through different zones. This is usually done via a conveyor system. The order is picked in the zone and transported via a conveyor belt to the next zone or to the shipping department. - Voice picking
With voice picking, an employee uses a headset that indicates which order he or she should take. This leaves both hands and eyes free. - Pick to light
Pick to light indicates where the order should be picked. The operator picks the article from the shelf and confirms this action with a button. - Picking trolley
The picking cart supports the warehouse worker in picking multiple orders. The software automatically calculates the optimal walking route, the optimal cart load and even gives advice on the cart structure.
Why is a smart warehouse management system (WMS) so important?
The ‘warehouse management system’ (WMS) is the brain behind all warehouse automation. A smart software system contributes to more efficient warehouse logistics. In addition, this system communicates with several intralogistics systems simultaneously, gives you exact information about your stock and calculates the most efficient route for order picking.
Reduce empty transport
A big challenge within intralogistics is the filling of empty space. For example, a too large box is used for an article, causing air to be transported; anything but sustainable and quite inefficient. Smart software offers the solution.
Link between ERP & WCS
A warehouse management system forms the link between the ‘enterprise resource planning’ system (ERP) and the ‘warehouse control system’ (WCS). On the basis of the information supplied by the ERP, the WMS controls the daily activities, such as order picking and the inbound and outbound transport of goods.
Automated Guided Vehicles (AGV) or Rail Guided Vehicles (RGV)
In many cases, software systems can also be connected to existing vehicles such as forklift trucks or special rail vehicles. These vehicles are then controlled by the software.
Costo Intralogistics offers several smart software systems which can also be connected to your existing warehouse logistics. Curious about how this connects to your warehouse logistics? You can read more about it here.
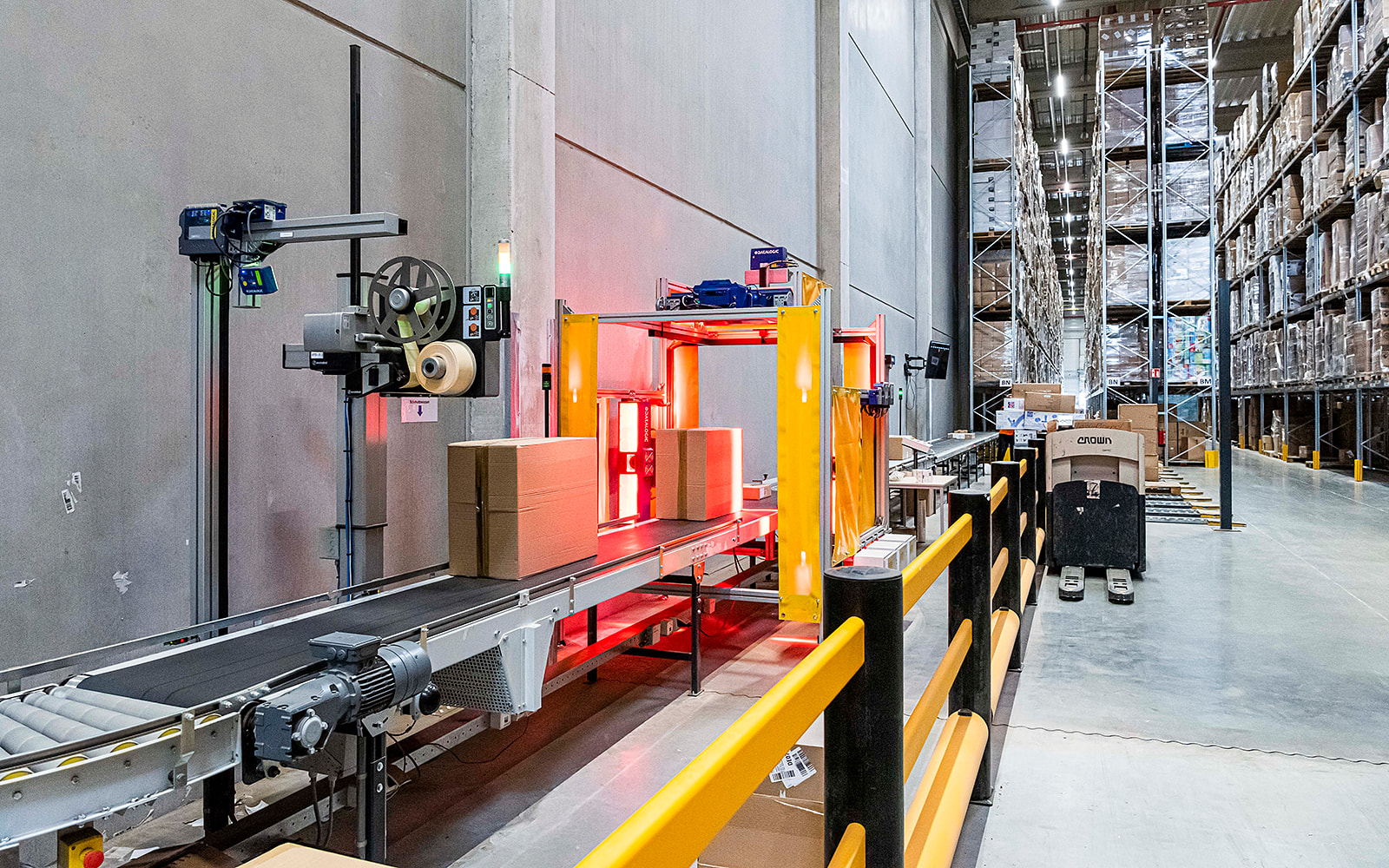
How does the maintenance for warehouse automation work?
When investing in warehouse automation, you naturally want the system to work at all times. This requires maintenance to guarantee a smoothly running system. If you have a system installed by Costo Intralogistics, we always offer a service agreement in which we make arrangements for maintenance.
For which warehouses is automation sensible?
Warehouse automation is applied more and more. Think about e-commerce, retail, production companies and logistics service providers.
Are you thinking about automating your warehouse? Then it is wise to first map out where the most profit can be made. Find out where the most mistakes are made and where the costs are the highest. If necessary, let an expert from Costo Intralogistics advise you on specific issues.
Costo Intralogistics, the specialist in automation of intralogistics
Do you have doubts about which automation solution is suitable for your warehouse? Our experienced team of experts is ready to help you! We offer a suitable solution tailored to the challenges of your unique warehouse.
Would you like to receive personal advice? Mail toinfo@costo-intralogistics.com or call us at +(31) 183-745045
COSTO Intralogistics expertise in practice.
Get inspired by one of our other projects!
Service and Support
Subscribe to our newsletter.
"*" indicates required fields