Case
Kobout.
Improving efficiency and speed with Arrow WMS.
More insight in the expected workload of the warehouse? Let’s discuss the possibilitie of a smart WMS!
Kobout, international supplier of fasteners.
Kobout has been an importer of fasteners since 1979. Kobout’s sales are focused on the European market. However, 80% of its purchases come from the Far East. In order to keep supply and transit routes flexible, Kobout is located in Hendrik-Ido-Ambacht, centrally located with a view to the ports of Rotterdam and Antwerp. The company has 10,000 m2 of warehouse space with 25,000 different SKUs. The inventory counts millions of items and is extremely diverse.
The challenge
Continuing to meet increasingly higher requirements.
Joost Kunst, Managing Director at Kobout, on the change in demand: “We are noticing more and more that our customers are making higher demands. Were in the past customers used to be satisfied with delivery in boxes, we are now receiving more and more requests at item level. This has given piece picking a more prominent role. The demand for value-added services has also grown strongly. Putting together kits or repackaging into private labels have become the rule rather than the exception.”
Kobout previously worked with a WMS module from the ERP system, but that was at its limit in terms of possibilities. With an eye on increasingly higher requirements and traceability, scanning and linking to existing systems, a full WMS was necessary.
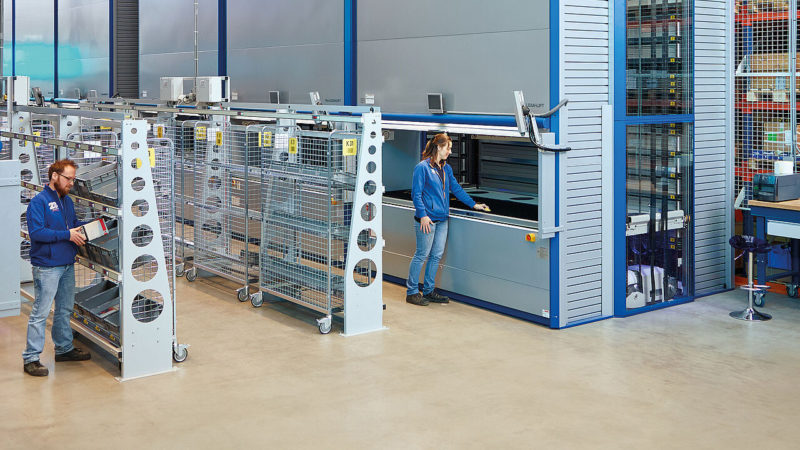
The solution
WMS determines storage location.
On a weekly basis, approximately 280,000 kilos of goods arrive. These were previously scanned manually, a time-consuming task. Now the WMS automatically determines where the articles can be stored. This saves a lot of time in normal weeks, especially when the quantities grow to some 400,000 kilos in peak periods!
Volledige traceerbaarheid
With the new WMS there is a complete traceability, which gives more insight into the expected workload in the warehouse.
Controlling platform lifts
The picking process works with 44 storage elevators from Hänel. Controlling these elevators is done in cooperation with the warehouse management system. The Arrow WMS of Costo has specific modules for controlling these platform elevators.
The result
Improvement in efficiency and speed through automation.
The WMS improves the efficiency and speed in various processes, both in storage and in the picking process. The automatic instead of manual allocation of incoming goods results in an enormous improvement in efficiency.
Because of the tracebility is able to switch faster if the available resources are not sufficient. Stocks can be replenished in time and orders will be shipped out on time.
In addition, the error rate will be reduced even further.
The WMS reinforces Kobout’s traditional strength. Now, Kobout can always deliver their rock-solid stock well and fast.
What customers say about us.
Costo Intralogistics has now set up several warehouses for us to our complete satisfaction. Their innovative ideas and flexibility play a major role in this for us.
Diana Burikina, support manager – Smyths toys, Walsrode (DE)
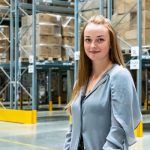
What stands out about Arrow WMS is its quality and flexibility. In addition, the reporting and visualization options of Costo are really nice to work with! This is definitely a plus in e-commerce: you want to be sure that the order arrives at the right time at the right place.”
Markus Kettenhofen, Site Manager Contract Logistics – Kuehne+Nagel
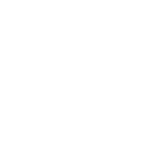
Thinking along with solutions so that we can meet our ultimate challenges, that is where Costo Intralogistics really stands out. Here you can immediately see the many years of logistics experience and expertise.
Maickel Versantfoord, managing director – Coldservice
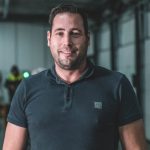
COSTO Intralogistics expertise in practice.
Get inspired by one of our other projects!