Case
Double win for efficiency.
Case: order picking and cross-docking over the same sorter at a logistics service provider.
Ready for more efficient orderpicking? Let’s discuss the possibilities!
The challenge
Serving the DIY industry flexibly:
Smarter cross-docking by a logistics provider, Willebroek (BE)
With space savings of more than 50%, a significant reduction of process errors, and improved efficiency in order picking, this logistics provider is ready for further growth.
The logistics provider wanted to investigate smarter cross-docking to benefit one of its customers in the DIY industry. Once the goods have arrived, a sorting plant helps to distribute them directly to the branches. The plant also sorts branch crates with collected orders. However as it turned out, the collection itself could also be done in a much smarter and more efficient way – an unexpected bonus.
The Solution
Goods -to-person.
Shuttle racks and AGV robots
Instead of a mezzanine floor with shelves that the order pickers have to find their way through, there are 1,100 movable shuttle racks, which together are good for 25,000 picking locations. Thanks to 32 flexible AMR robots of Eiratech Robotics, the racks move automatically. Put and pick to light are used for entry and exit through six workstations, with collectors concentrating on picking rather than walking and searching.
1500 Units per hour
Branch orders are transferred from the shuttle racks into plastic crates that are then transported by conveyors to the sorting plant, where they are distributed by branch. The plant has a capacity of 1,500 units per hour, with 14 chutes, each of which represents up to 10 branches. The goods are distributed into roll containers or onto pallets here, using put to light.
Double the benefit
The sorting plant processes outbound crates of store orders in the morning, and in the afternoon it’s ready for the cross-docking process, in which it distributes incoming pallet loads directly to the branches.
Image credits: Eiratech Robotics.
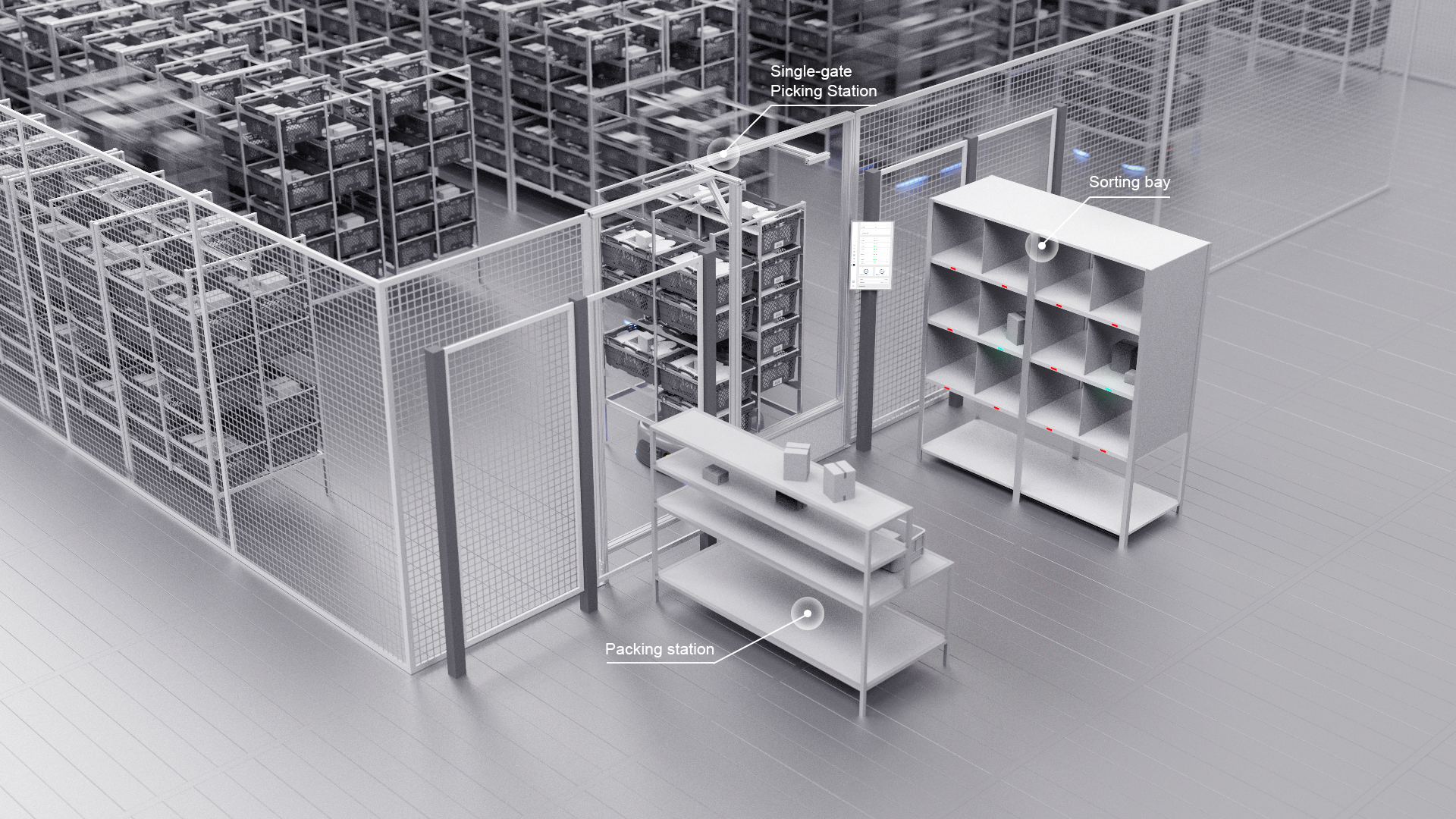
The result
A double win in terms of efficiency and space savings.
Walk less, work smarter
The logistics service provider saves a great deal of space thanks to this Costo total solution, which includes a link to the ERP. It can now benefit from more storage locations over less than 50% of the original floor space. The goods-to-person principle means that the average output of a collector is 450 lines per hour – higher than before, and with a decreased chance of errors. The space gained makes room for storing other products, increasing the market opportunities for both the logistics provider and the customer.
The double function of the sorting installation proves daily the convenience of automatic distribution and timely delivery to the branches of the DIY stores in the Benelux.
What customers say about us.
Costo Intralogistics has now set up several warehouses for us to our complete satisfaction. Their innovative ideas and flexibility play a major role in this for us.
Diana Burikina, support manager – Smyths toys, Walsrode (DE)
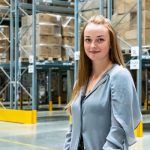
What stands out about Arrow WMS is its quality and flexibility. In addition, the reporting and visualization options of Costo are really nice to work with! This is definitely a plus in e-commerce: you want to be sure that the order arrives at the right time at the right place.”
Markus Kettenhofen, Site Manager Contract Logistics – Kuehne+Nagel
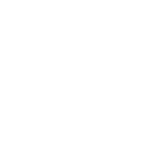
Thinking along with solutions so that we can meet our ultimate challenges, that is where Costo Intralogistics really stands out. Here you can immediately see the many years of logistics experience and expertise.
Maickel Versantfoord, managing director – Coldservice
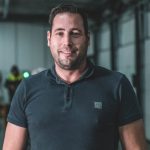
COSTO Intralogistics expertise in practice.
Get inspired by one of our other projects!