Case
President Safety.
Wholesale
Ready for a futureproof warehouse? Let’s discuss the possibilities!
President Safety, Oud-Gastel (NL)
A future-proof warehouse.
As a wholesaler of personal protective equipment (PPE), President Safety quickly grew into an established name in Europe. The company has seen great demand for their products in recent years and foresees this demand only increasing further. This is accompanied by the need for a future-proof warehouse. Peter Hoendervanger, logistics manager at President Safety, talks more about the intralogistics challenges in their warehouse and the cooperation with Costo.
The challenge
Setting up a smart warehouse in Oud-Gastel.
Due to growth, President Safety moved in to new premises in Oud-Gastel. With this new location, President Safety has plenty of room to grow further. Peter explains: “To create sufficient capacity for our expected growth, we were looking for a new location for a warehouse. We are known in the market as a reliable party that delivers quickly and keeps sufficient stock. We export to countries all over Europe, including the Benelux, but also to countries such as Germany, Poland and France. We currently process between 150 and 200 orders per day in Oud-Gastel. We expect this to grow quickly to 500 orders per day. Our old warehouse in Hellevoetsluis quickly became too small for this. Hence, we moved to Oud-Gastel in 2022 and engaged Costo to help us with the warehouse automation.”
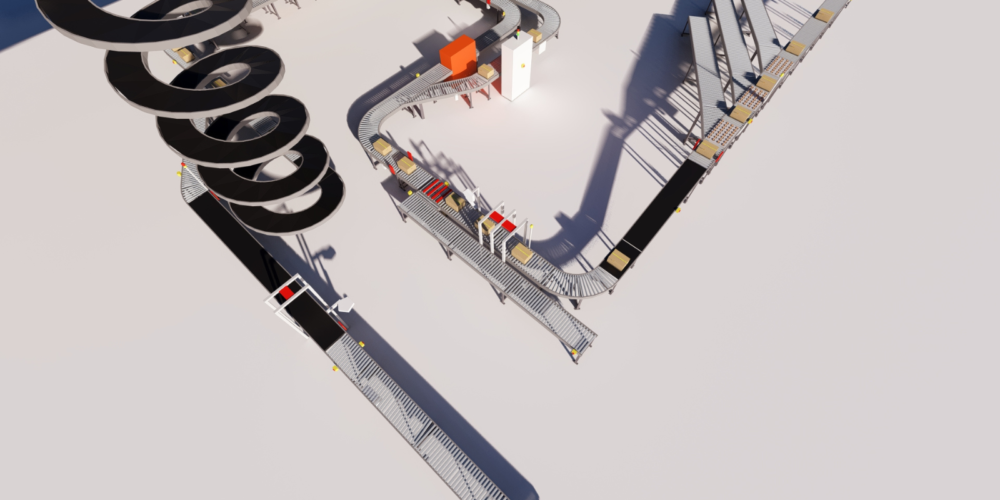
The solution
Complete warehouse automation with integration on SAP ERP system.
President Safety was looking for a warehouse management system (WMS) with integration on the SAP ERP system. This provides better visibility of stock and all data, allowing President Safety to better manage stock and orders. In addition, the company was looking for complete warehouse automation that works well with the software. “In the past, everything was done manually. This is labour-intensive and error-prone. In the new warehouse, we have a conveyor belt that allows us to get the right products to the right location and take care of the handling from the picking process faster. We also have better overall control over intralogistics. Currently, only four to five employees work in logistics. With automation, it remains possible to process orders with this team.”
Check out President Safety’s sleek warehouse.
The result
A warehouse full of possibilities for the future.
Purchasing the warehouse software and hardware from one party gives advantages, according to Peter. “Because we use Costo’s conveyor belt and software, we get all the conveniences from the system to switch quickly. Our stock has doubled compared to our old warehouse. This strengthens our image as a reliable supplier, because we almost always deliver from stock. Moreover, the risk of errors is lower. This is partly due to automatic labelling of boxes. The warehouse software and hardware, combined with the warehouse space, increases our capacity to around 600 to 1,200 orders per day.
More control with the Warehouse Management System.
There is also much more control over the system, allowing us to work more accurately. This is partly due to the integration with our ERP system. The picking and storage process is controlled from the Arrow warehouse management system (WMS). Purchasing, order processing and invoicing are done in the ERP system.”
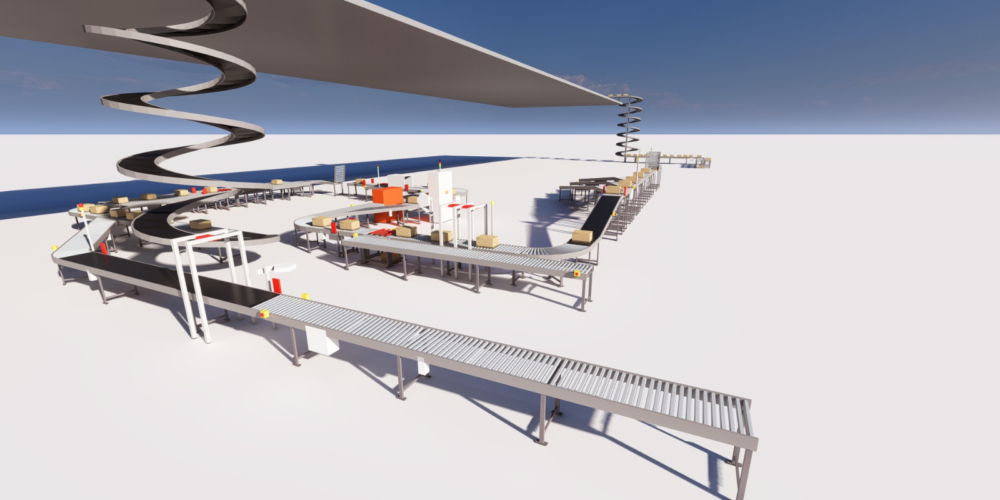
Costo as intralogistics partner
Thinking in terms of solutions.
The choice fell on Costo’s total solution because of good past experiences. “We have known Costo for a long time and in previous collaborations Costo has proven itself. Because of this, the choice for Costo was quickly made. We knew in advance that it was a difficult time to get parts and materials. Initially, the aim was to go live as early as March. Due to setbacks in the availability of materials, this became difficult. By working together with Costo to look at possibilities to make the conveyor belt work for the time being, we were able to continue for the time being. The automation is now fully operational and it was well worth the wait.”
Coming up with creative solutions together for now and the future.
In addition to current solutions, the system offers flexible expansion options. “The beauty of this system is its modularity. We can expand the system if demand picks up further, without it meaning the warehouse comes to a complete standstill. In the future, we can, for example, install another system for automatically sealing boxes and a system to get the right size boxes. In summary, Costo is a party that thinks with you and with whom you arrive at creative solutions together.”
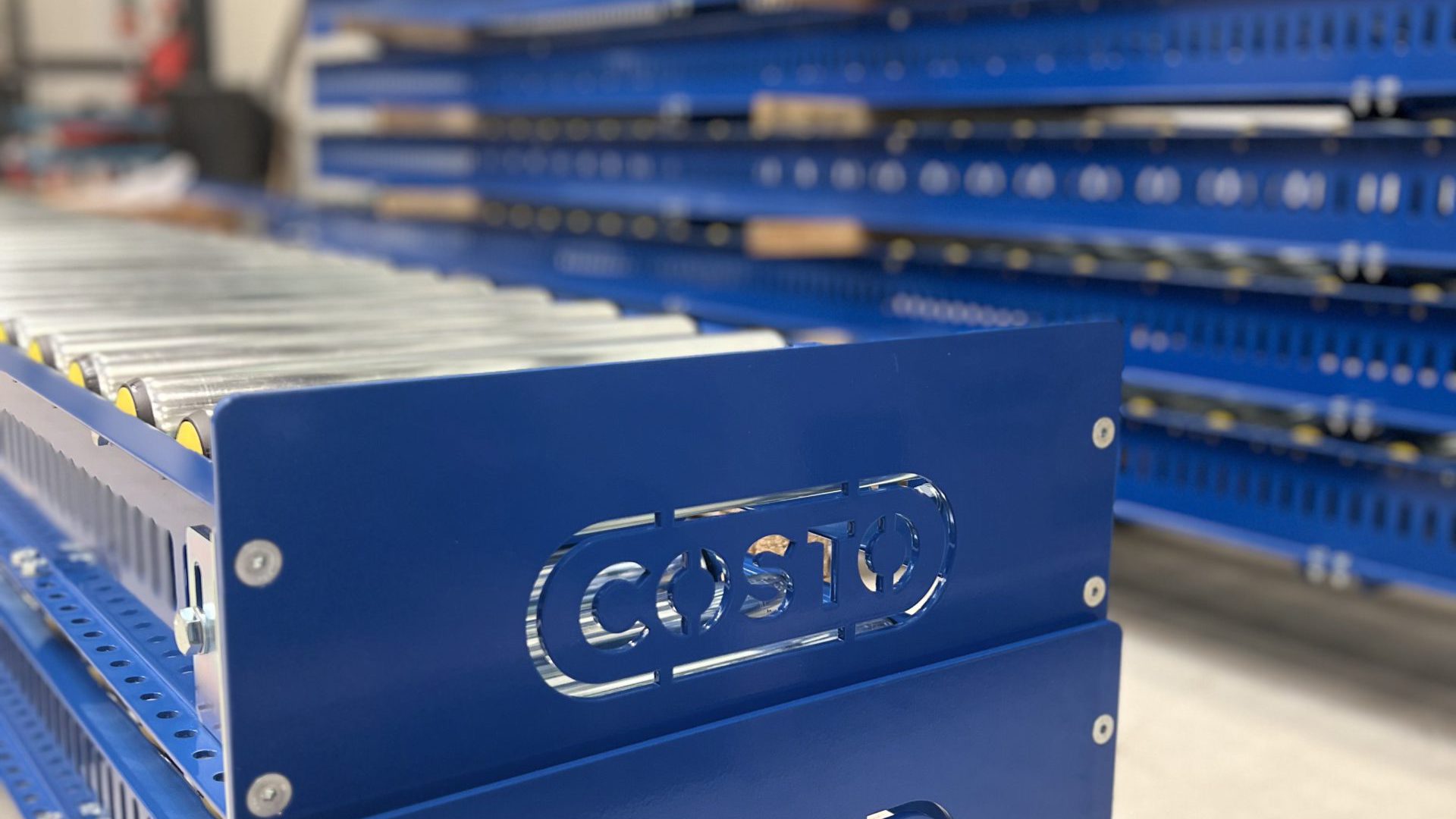
What customers say about us.
Costo Intralogistics has now set up several warehouses for us to our complete satisfaction. Their innovative ideas and flexibility play a major role in this for us.
Diana Burikina, support manager – Smyths toys, Walsrode (DE)
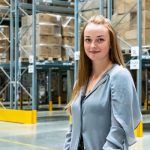
What stands out about Arrow WMS is its quality and flexibility. In addition, the reporting and visualization options of Costo are really nice to work with! This is definitely a plus in e-commerce: you want to be sure that the order arrives at the right time at the right place.”
Markus Kettenhofen, Site Manager Contract Logistics – Kuehne+Nagel
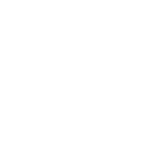
Thinking along with solutions so that we can meet our ultimate challenges, that is where Costo Intralogistics really stands out. Here you can immediately see the many years of logistics experience and expertise.
Maickel Versantfoord, managing director – Coldservice
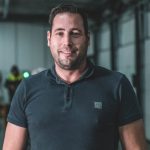
COSTO Intralogistics expertise in practice.
Get inspired by one of our other projects!